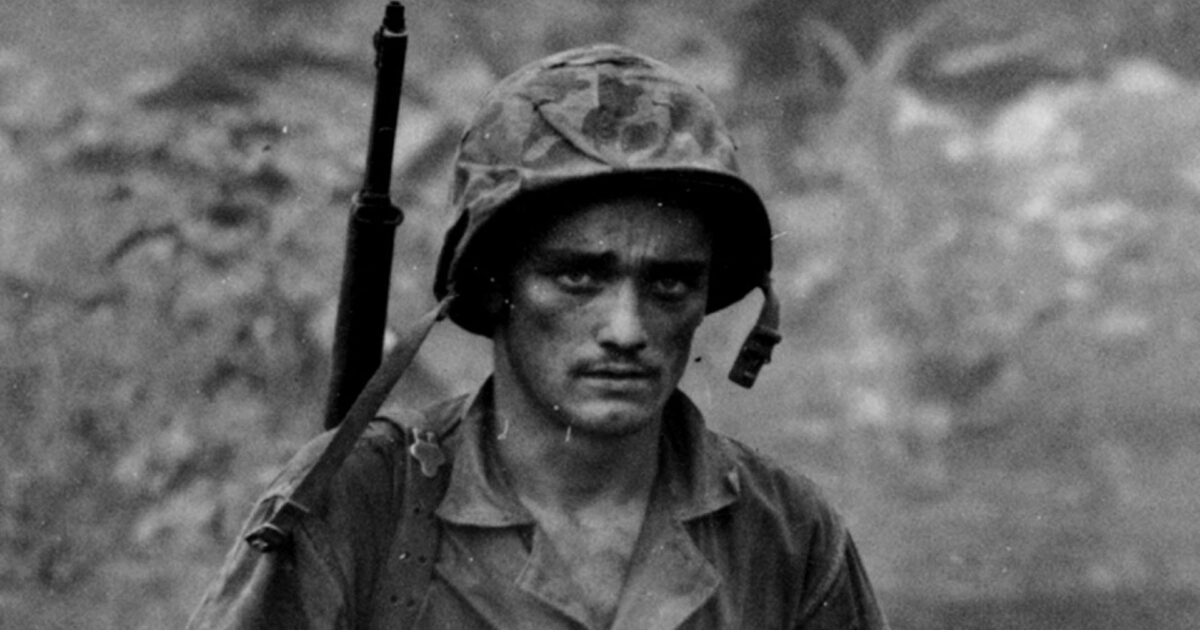
In the three years following the Battle of Midway, the Japanese built six aircraft carriers. The U.S. built 17. American industry provided almost two-thirds of all the Allied military equipment produced during the war: 297,000 aircraft, 193,000 artillery pieces, 86,000 tanks and two million army trucks. In four years, American industrial production, already the world's largest, doubled in size.
“Powerful enemies must be out-fought and out-produced,” President Franklin Roosevelt told Congress and his countrymen less than a month after Pearl Harbor. “It is not enough to turn out just a few more planes, a few more tanks, a few more guns, a few more ships than can be turned out by our enemies,” he said. “We must out-produce them overwhelmingly, so that there can be no question of our ability to provide a crushing superiority of equipment in any theatre of the world war.”
Two years earlier, America’s military preparedness was not that of a nation expecting to go to war. In 1939, the United States Army ranked thirty-ninth in the world, possessing a cavalry force of fifty thousand and using horses to pull the artillery. Many Americans — still trying to recover from the decade-long ordeal of the Great Depression — were reluctant to participate in the conflict that was spreading throughout Europe and Asia. President Roosevelt did what he could to coax a reluctant nation to focus its economic might on military preparedness. If the American military wasn’t yet equal to the Germans or the Japanese, American workers could build ships and planes faster than the enemy could sink them or shoot them down.
In the wake of Pearl Harbor, the president set staggering goals for the nation’s factories: 60,000 aircraft in 1942 and 125,000 in 1943; 120,000 tanks in the same time period and 55,000 antiaircraft guns. In an attempt to coordinate government war agencies Roosevelt created the War Production Board in 1942 and later in 1943 the Office of War Mobilization. To raise money for defense, the government relied on a number of techniques — calling on the American people to ration certain commodities, generating more tax revenue by lowering the personal exemption and selling government war bonds to individuals and financial institutions. All of these methods served to provide the government with revenue and at the same time keep inflation under control.
War production profoundly changed American industry. Companies already engaged in defense work expanded. Others, like the automobile industry, were transformed completely. In 1941, more than three million cars were manufactured in the United States. Only 139 more were made during the entire war. Instead, Chrysler made fuselages. General Motors made airplane engines, guns, trucks and tanks. Packard made Rolls-Royce engines for the British air force. And at its vast Willow Run plant in Ypsilanti, Michigan, the Ford Motor Company performed something like a miracle 24-hours a day. The average Ford car had some 15,000 parts. The B-24 Liberator long-range bomber had 1,550,000. One came off the line every 63 minutes.
America launched more vessels in 1941 than Japan did in the entire war. Shipyards turned out tonnage so fast that by the autumn of 1943 all Allied shipping sunk since 1939 had been replaced. In 1944 alone, the United States built more planes than the Japanese did from 1939 to 1945. By the end of the war, more than half of all industrial production in the world would take place in the United States.
Wartime production boomed as citizens flocked to meet the demand for labor. Tensions were often high between labor unions, which in spite of no-strike pledges felt the need to protect worker’s rights and could not stop strikes altogether, and citizens were outraged to hear of any work stoppages. In one instance when the United Mine Workers went on strike in 1943, newspapers condemned the miners as traitors. On June 25, 1943, Congress passed the War Labor Disputes (Smith-Connally) Act that authorized the President to take over plants needed for the war effort or in which war production had ceased because of a labor dispute.
While 16 million men and women marched to war, 24 million more moved in search of defense jobs, often for more pay than they previously had ever earned. Eight million women stepped into the work force and ethnic groups such as African Americans and Latinos found job opportunities as never before.
“Most of the people who got out of high school if they were female and didn’t go to the war, they went to Mobile,” said Emma Belle Petcher, who moved to the city from the tiny town of Millry, Alabama. “That was the place to go and get a job. And there were all kinds of jobs.”
World War II utterly transformed Mobile and its economy. The explosion began in the late 1930s, when local companies such as Alcoa began producing war materiel for Japan and European countries. Local shipyards won contracts to build Liberty ships and destroyers in 1940, and by the time America entered the war in late 1941, Mobile was already booming. The Alcoa plant processed millions of pounds of alumina used to build many of the 304,000 airplanes America produced during the war; the Waterman Steamship Company boasted one of the nation’s largest merchant fleets, and Mobile became one of the busiest shipping and shipbuilding ports in the nation. In 1940, Gulf Shipbuilding had had 240 employees; by 1943, it had 11,600. Alabama Dry Dock went from 1,000 workers to almost 30,000.
Like the shipyards in Mobile and plane-repair facilities near Sacramento, factories in Waterbury, Connecticut were transformed to keep up with the war. The Mattatuck Manufacturing Company switched from making upholstery nails to cartridge clips for the Springfield rifle, and soon was turning out three million clips a week. The American Brass Company made more than two billion pounds of brass rods, sheets and tubes during the war. The Chase Brass and Copper Company made more than 50 million cartridge cases and mortar shells, more than a billion small caliber bullets and, eventually, components used in the atomic bomb.
Scovill Manufacturing produced so many different military items, the Waterbury Republican reported, that “there wasn’t an American or British fighting man … who wasn’t dependent on [the company] for some part of the food, clothing, shelter and equipment that sustained [him] through the … struggle.”
Many factories ran around the clock. “It was seven days a week,” said Clyde Odom of Mobile. “And during the war when it was so strong, it was twelve-hour days five days a week, ten hours on Saturday, eight hours on Sunday, you felt like you've had a week off. And that went in and out, over, over and over and over.”
“Money seemed to be the least of the concerns,” Ray Leopold of Waterbury said. “The thing was to produce material that will win the war and bring their boys home.”
With the economy booming, Americans felt their lives improving.
“Things started getting better and better and better for the people who had to stay behind,” Sacramento’s William Perkins said. “People were doing real good economically. And it was a big boost from the end of the Depression up until the war ended and it just rolled on.”
ncG1vNJzZmivp6x7sa7SZ6arn1%2Bgsq%2Bu1KulrGeknbJuw8CrZrCZomK9s7vDrpqtoZ%2Bj